Boiler equipment
- subcritical pressure boilers for 150 MW units and under (up to 500 t/h);
- subcritical pressure boilers for 225 MW units;
- supercritical pressure boilers for 300 MW units;
- supercritical pressure boilers for 660-800 MW units;
- supercritical pressure boilers for 1200 MW units;
- incinerators for various types of biomass (wood chips, straw pellets, husks) of differing steam capacity.
- heat-recovery steam generators for small power installations (2.5 to 60 MW);
- heat-recovery steam generators for 300 MW units and under;
- heat-recovery steam generators for 800 MW combined-cycle power units CCGT and under;
- heat-recovery steam generators for oil production.
- collector- and coil-type high-pressure heaters;
- simple high-pressure heaters;
- steam coolers.
- low-pressure heaters;
- water coolers;
- mainline water heaters;
- surface-type evaporators and steam transformers;
- vacuum turbine condensers;
- water heat exchangers;
- steam-water heaters;
- deaerators.
- clarifying filters;
- sorption filters;
- ionite filters.
The Taganrog boilermaking factory Krasny Kotelshchik has extensive experience in the design and operation of boilers using fuels that have traditionally been regarded as difficult to use in the power industry, such as anthracite and anthracite fines, Ekibastuz coal and lignite.
- company engineers’ participation in the testing and commissioning of boiler units and their components, local equipment examination at power plants;
- hydraulic, aerodynamic and strength testing of full-scale models of critical equipment components at the factory’s benches;
- aerodynamic research using physical models;
- geometric 3D modeling of various boiler systems;
- multivariant calculations utilizing mathematical modeling and design analysis using a super computer.
- high efficiency and the potential for its increase;
- a proven design base including the existing capabilities of the manufacture and delivery of high-pressure (HP) boilers, supercritical-pressure (SCP) boilers and super-SCP boilers with initial level performance;
- the potential for further development in promising areas (circulating fluidized bed (CFB), etc.), combined with other technologies (combined-cycle units, gas generation);
- a proven process and material base (steels, tubes, forgings) including the existing capabilities of the manufacture and delivery of HP boilers, SCP and super-SCP boilers with further development in promising areas;
- the capability for integrated work on the improvement of all steam-boiler components as the main parts of steam turbine units to increase cost-effectiveness and reduce the costs of auxiliary equipment operation;
- the potential for further increase in the single unit capacity of steam boiler units, power units and thermal power plants as a whole;
- the potential for the use of new technologies for combustion chamber and other boiler processes;
- the potential for the use of boiler units in various combinations with gas turbine technologies, in various types and designs of combined-cycle (CCGT) units (ranging from CCGT units with GT gas discharge to solid fuel boilers to the design of a CC unit with gas generation using solid fuel and with an HRSG downstream for the gas turbine).
The entire boiler unit conforms to the strictest international requirements and Russian quality standards and has all the certificates and permits necessary for commissioning according to the requirements of the regulatory authorities of the Russian Federation.
- does not require circulation pumps for HRSG start-up and operation;
- reduces balance-of-plant power consumption;
- requires fewer spare parts and less maintenance;
- the boiler design is highly modular;
- utilizes a lightweight modular structure;
- self-supporting stack and a self-supporting stair tower adjacent to the boiler;
- the horizontal structure with natural circulation is compact and has dimensions similar to those of vertical boilers. At the same time, horizontal boilers are more cost-effective, more reliable and easier to maintain.
The compact dimensions of a horizontal HRSG allow it to be installed within the dimensions of a vertical HRSG, which makes the boilers a universal solution for the customer – even if construction or modernization operations take place in limited space conditions.
The use of an afterburner makes it possible to ensure the required steam parameters downstream of the HRSG if these parameters are not ensured by gas-turbine exhaust gases due to climatic or seasonal conditions or gas-turbine-type specifics.
Main design modules and boiler components operating under pressure and requiring special monitoring are selected for diagnostics. “High-temperature” and “low-temperature” boiler components are regarded separately. The difference between unheated and heated components is also taken into account. The ABDS enables the diagnostics of the entire boiler.
- stamped-and-welded branches with a diameter of 530-1420 mm and rotation angles of 30-90°, for a maximum pressure of 9.8 MPa and a pressure of 11.8 MPa;
- stamped-and-welded T-pieces with a diameter of 530-1420 mm with drawn necks with diameters of 219-1420 mm with or without grills, with a maximum pressure of 9.8 MPa and a pressure of 11.8 MPa;
- welded T-pieces with diameters of 530-1420 mm with welded necks with various diameters up to 1420 mm with or without grills, with a maximum pressure of 9.8 MPa;
- stamped heads with diameters of 530-1420 mm for a maximum pressure of 9.8 MPa and a pressure of 11.8 MPa;
- reducer rings with diameters of 530-1420 mm for a maximum pressure of 9.8 MPa and a pressure of 11.8 MPa.
1. Installation and adjustment services for supplied equipment.
2. Full package of equipment maintenance services throughout the lifecycle based on:
- long-term customer service contracts (6-12 years);
- the implementation of remote condition-monitoring systems;
- the development and provision of maintenance and repair services based on actual running hours and failure criticality level;
- the development and provision of long-term equipment maintenance, repair and modernization programs covering the entire lifecycle.
3. Responsibility for technical and economic performance and equipment availability.
- heated surfaces (combustion chamber screens, convection- and platen-type steam superheaters, water economizers);
- spare parts for regenerative air heaters (RAH);
- high-, medium- and low-pressure drums;
- burner devices;
- manifolds and steam coolers;
- spirals for high-pressure heaters;
- pressure safety, control, check, shutoff valves;
- quick-acting protection devices;
- manual valves;
- water level gages;
- oil coolers;
- level control devices;
- vessels (oil-air, air, equalizing);
- distribution pipes.
Catalogues
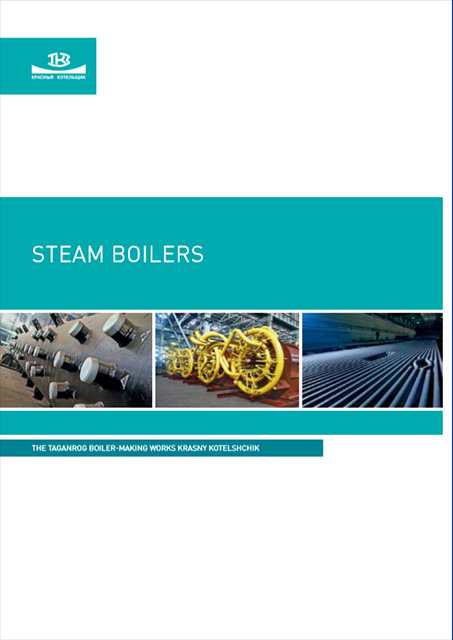
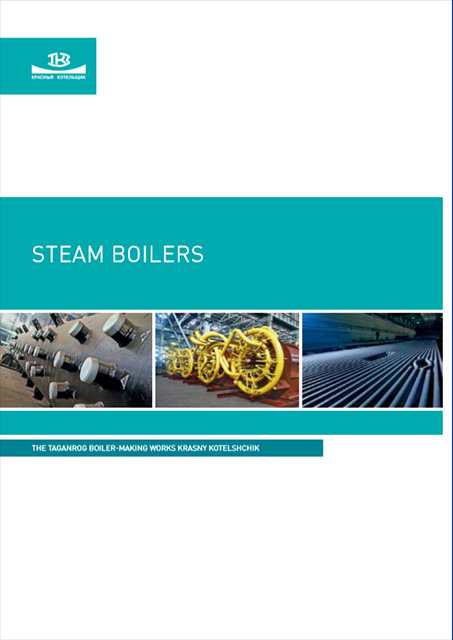
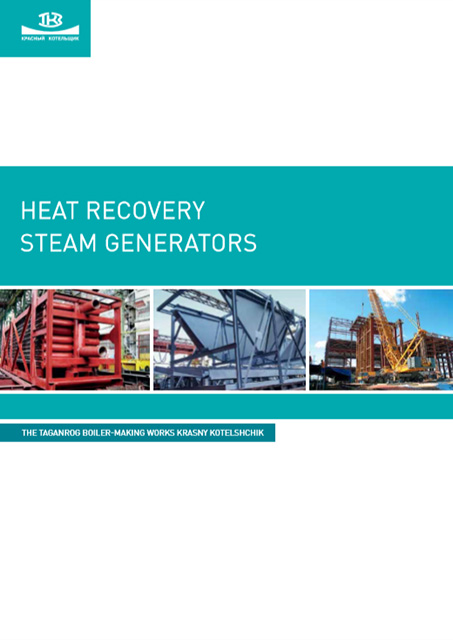
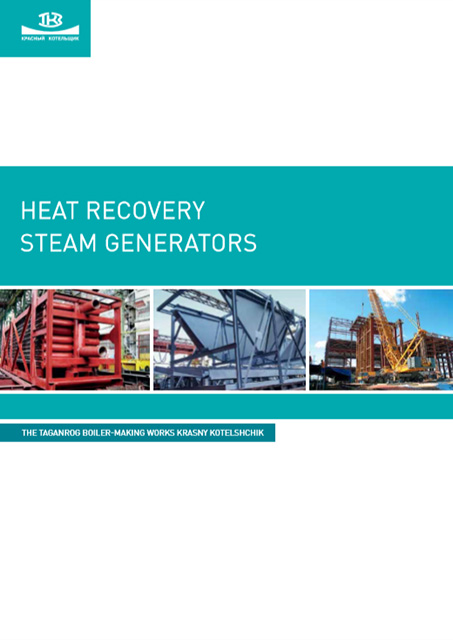
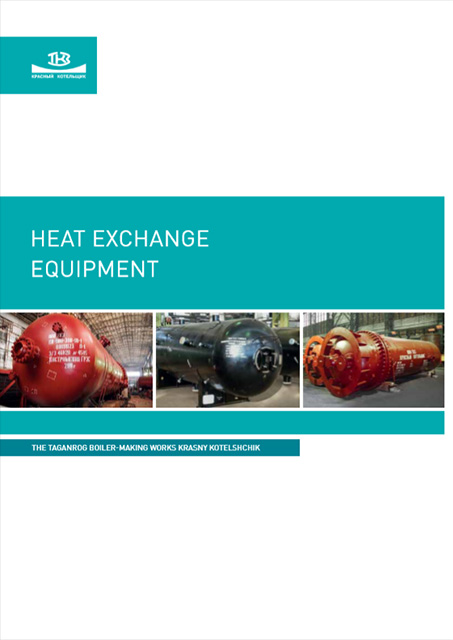
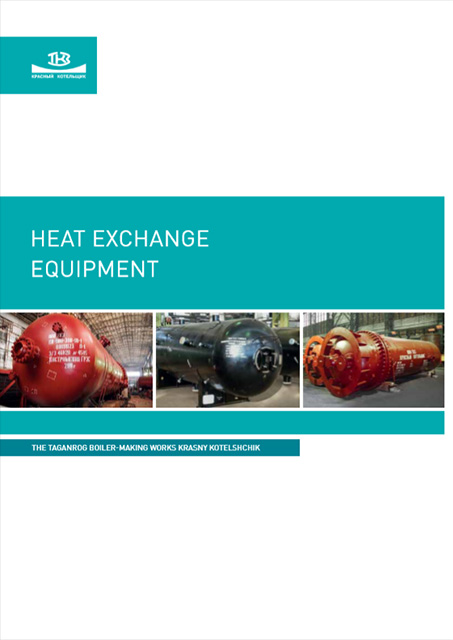
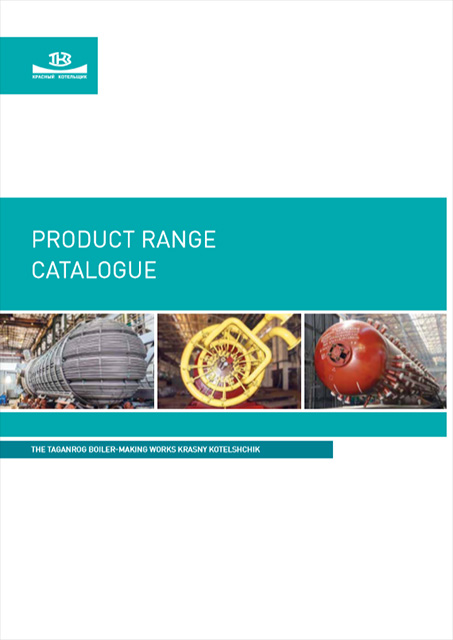
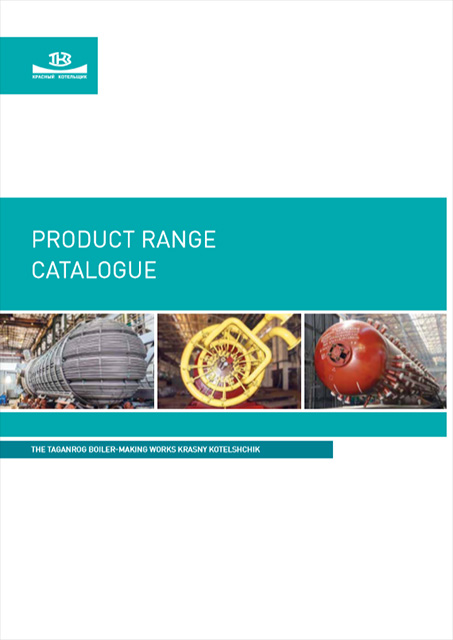
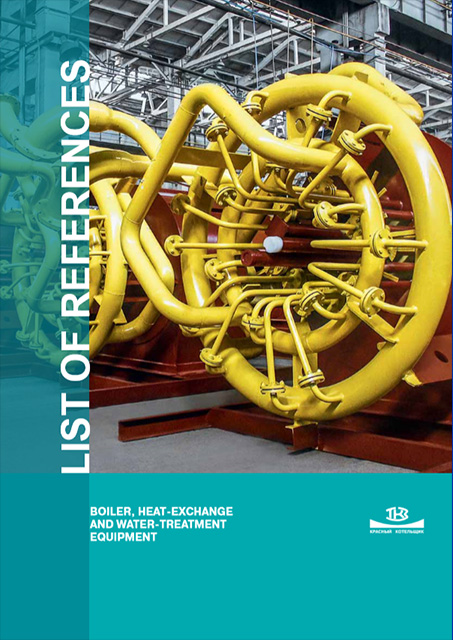
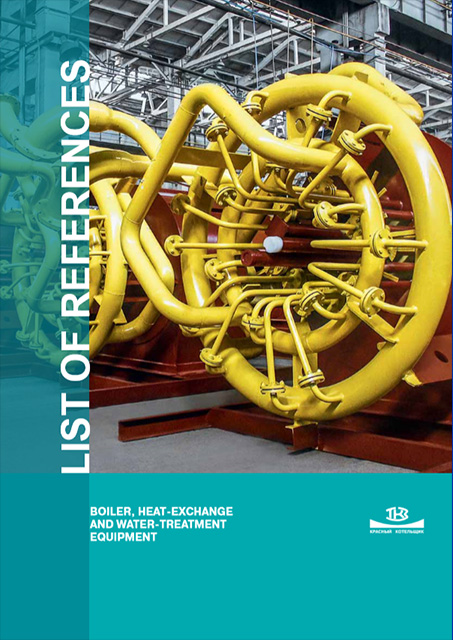
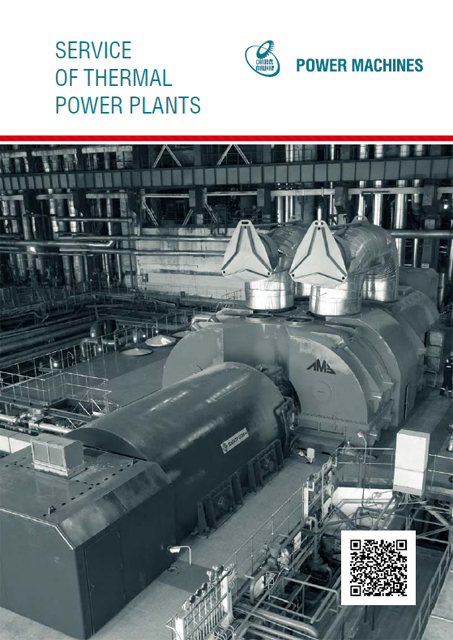
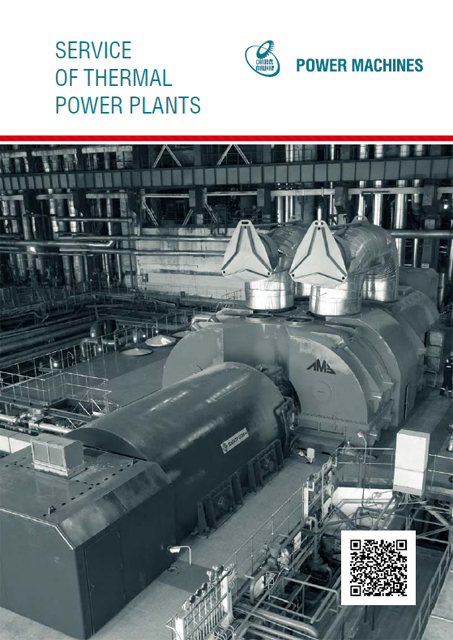