Steam turbines
К-1200-240 | К-800-240 | - |
К-660-247 | К-500-240 | К-500-166-1(2) |
К-330-240 | К-300-170 | ТК-330-240 |
К-300-170-1Р | К-330-23,5-2Р | К-255-162 |
К-225-12,8-3Р(4P) | К-225-12,8 | К-225-12,8-3 |
К-215-130-1(2) | К-210-130-8 | К-200-181 |
Т-185-12,8-1(2) | Т-180-130-1(2) | Т-185/210-16,0-Р |
К-165-130 | Т-150-7,7 | К-160-7,5 |
К-110-6,5 | Т-140-145 | Т-130/160-12,8 |
Т-120/140-12,8 | Т-115-8,8 | Т-120-12,8 |
КТ-115-8,8-2 | КТ-120-8,8-2M | КТ-120-12,8 |
К-110-140 | К-100-90 | - |
ПТ-80-130 | ПТР-80-130 | К-80-7,0 |
ПТ-65-130 | ПТ-65-90 | Т-60-112 |
Р-25-8,8-1(2) | Р-50-90(130) | Р-85-8,8 |
К-55-90 | К-55-60 | Т-50-8,8 |
К-40-62 | ПТ-30-8,8 | ПТ-40/50-8,8 |
ПР-30-2,9 | ПТР-30-2,9 | ПТ-30-3,4 |
ПТ-30-2,9 | ПТ-35/55-3,2 | Т-30-2,9 |
Т-25-3,4 | П-30-2,9 | - |
In terms of flow-path characteristics, our turbines have a level of efficiency equal to that of turbines by the leading global manufacturers. Long-term experience of turbine operation makes it possible to guarantee reliable turbine operation for more than 40 years and a mean time between failures of at least 6 years.
The impressive cost-effectiveness and reliability of Power Machines steam turbines are ensured by:
- aerodynamic pilot testing of blades to confirm their reliability and efficiency;
- smooth meridional profiles of flow paths;
- blade design checks by CFD methods;
- 3D profiling of guide vanes;
- steam inlet, bleed and exhaust optimization using CFD methods;
- new improved seal designs;
- the implementation of advanced design methods, as well as technologies and equipment from leading Russian and global manufacturers.
Losses are reduced thanks to the use of high-performance blading, state-of-the-art types of seals, advanced water removal from low-pressure flow path structure and an improved regenerative heater system.
Blades of all stages have integrally-machined shrouds, which improves stage reliability and performance. Power Machines specialists have developed and implemented new types of highly-effective seals that ensure the reduced outer clearances of blades and provide reduced leakage.
Power Machines approaches new equipment development in accordance with the overarching power-engineering trend – continuous efficiency improvement through increases in initial steam conditions and turbine design enhancement.
The modular design principle is used for steam turbine construction, based on the use of major components, such as cylinders, stage groups, separate stages, rotors, housings, bearings, etc. Major turbine components have a high level of structural and process optimization and proven operating performance. Such an approach makes it possible to design new structures using all the best practices accumulated as a result of the operation of an extensive park of prototype turbines and to reduce project execution time.
- turbogenerators of various types with a maximum capacity of 1200 MW;
- boiler equipment, such as utility boilers, heat-recovery steam generators, auxiliary heat-exchange equipment, etc.;
- electrical automation systems;
- auxiliary equipment, such as condensers, oil coolers, gland steam condensers, bleed check valves, filters, etc.
Power Machines offers a complete service package for the installation supervision, adjustment supervision and testing of power equipment to be put into operation; modernization, repair and renovation works; the supply of spare parts and special materials.
The customer services provided by Power Machines include the engineering supervision of power-equipment installation, adjustment and commissioning; as well as warranty services, participation in scheduled maintenance, repair process development, customers’ and contractors’ personnel training, consulting services and post-warranty services.
- full or partial modernization of high-, intermediate- and low-pressure cylinders with or without steam-flow rate buildup in order to increase power and efficiency by 2 to 12% and reduce specific fuel consumption by 3 to 10% (depending on the scope of the overhaul, initial equipment condition and local conditions);
- process extraction steam turbine modernization in order to increase their throughput due to reduced steam consumption for production purposes;
- turbine overhaul in order to adapt the main and auxiliary equipment of the unit to the combined cycle;
- the provision of additional extractions from high-, intermediate- or low-pressure cylinders of 60 to 300 MW turbines to meet customers’ requirements in process and heating steam extractions;
- the installation of 25 to 70 MW supplementary turbines utilizing unused process bleed steam;
- the provision of controlled heating-steam extractions for 200 to 1200 MW condensing turbines to achieve a thermal power of 100 to 300 Gcal/h;
- the modernization of valves, steam distribution and control systems;
- the modernization of control, vibration monitoring and diagnostics systems;
- process control system modernization with a transition to electronic systems;
- condenser replacement and auxiliary equipment enhancement.
Catalogues
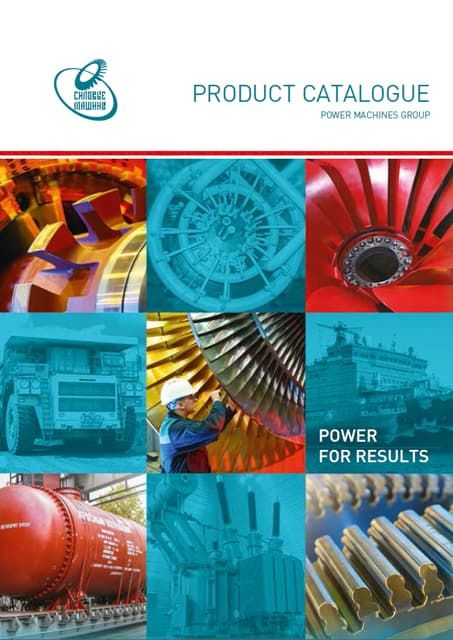
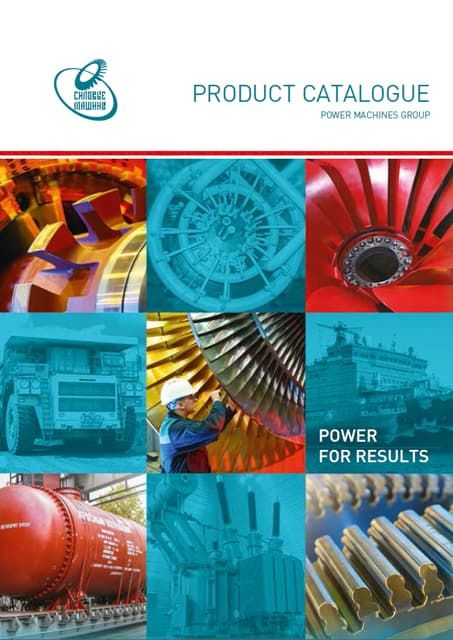
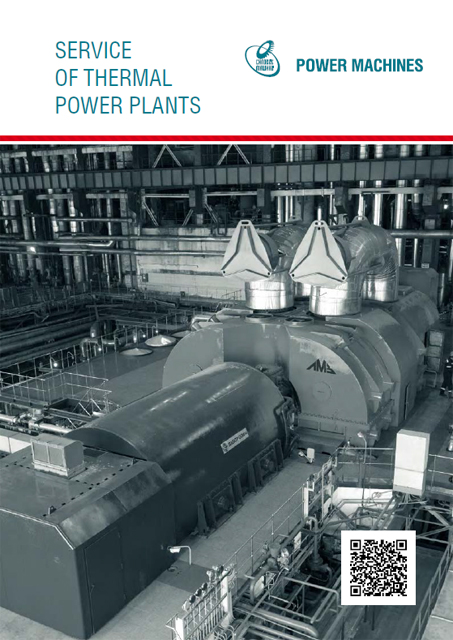
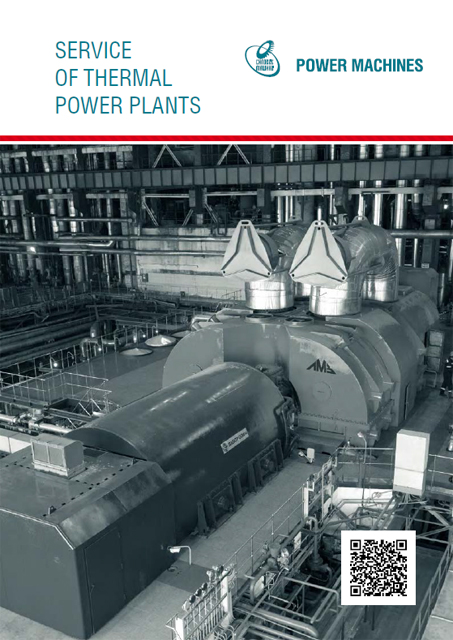
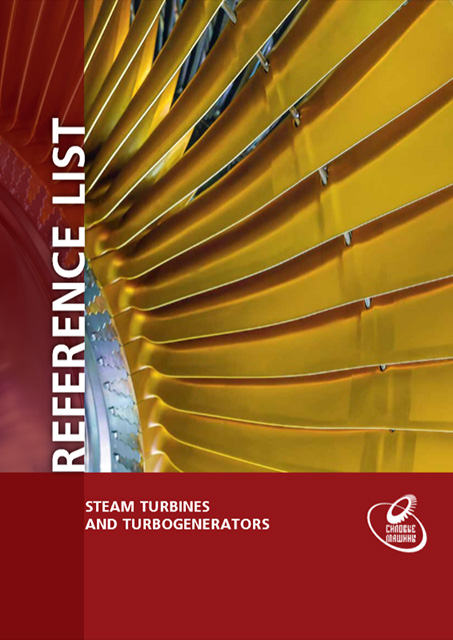
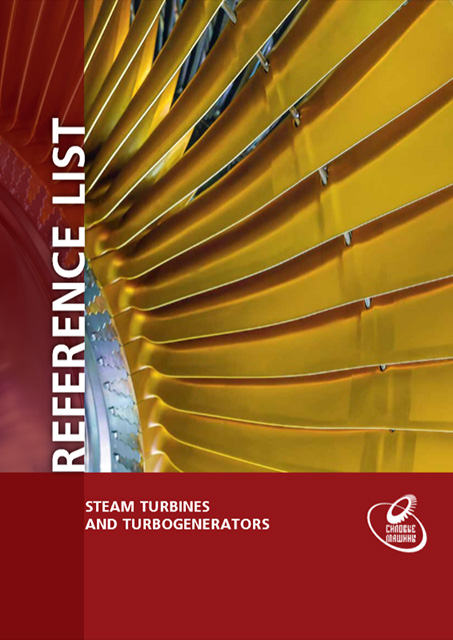