Hydrogenerators
Power Machines’ hydrogenerators are manufactured at the Electrosila factory. The first Russian hydrogenerator was made in 1924. As of today, more than 650 hydrogenerators have been manufactured, with a total capacity of over 65.5 GW.
The product line includes generators with a capacity of 4 to 720 MW and rated speeds of 50 to 750 RPM, for a wide range of voltages of 3.15 to 18 kV, for 50 and 60 Hz mains. Various excitation and cooling systems are also used.
Generator types:
- vertical indirect air-cooled hydrogenerators with a maximum capacity of 420 MW;
- vertical hydrogenerators with stator winding water cooling and a maximum capacity of 720 MW for HPPs;
- bulb hydrogenerators with forced-air cooling and a maximum capacity of 54 MW for HPPs;
- high-speed hydrogenerators with a maximum rated speed of 750 RPM;
- hydrogenerators with a capacity of over 4 MW for small HPPs.
The design of Power Machines’ hydrogenerators allows for easy access during installation and maintenance, ensures high reliability, reparability and environmental safety. The hydrogenerators produced by Elektrosila are highly competitive and reliable and have an extended service life thanks to the following advantages:
- a wide range of hydrogenerators (vertical, horizontal, bulb-type);
- a wide capacity (4 to 720 MW), voltage (up to 18 kV);
- and speed (55 to 750 RPM) ranges;
- various cooling technologies (air and water-based);
- the manufacture of new and overhaul of existing hydrogenerators;
- expansion of the reactive power consumption area;
- reduced weight and dimensions and efficient utilization of the hydrogenerator’s active volume;
- increased efficiency;
- the launch of new product types (motor hydrogenerators for pumped storage power plants, motor hydrogenerators for tidal power plants, hydrogenerators with a maximum capacity of 1000 MW).
The impressive cost-effectiveness and reliability of Power Machines’ hydrogenerators are ensured by:
The use of state-of-the-art materials:
- materials for thermosetting stator winding insulation;
- stator cores are made of state-of-the-art electrical steels;
- state-of-the-art epoxy varnishes;
- non-magnetic rotor pole pressure jaws;
- PTFE coating of thrust bearing and other bearing segments.
The use of state-of-the-art technology:
- vacuum-pressure impregnated rotor poles;
- soldered excitation windings;
- laser-cut rotor rim segments;
- stator core assembly “into a ring” at the installation location using hot stator core pre-tension.
State-of-the-art calculation tools are used during design and R&D stages, including computer-aided calculations utilizing leading software, and the computer-aided preparation of design drawings.
Our company is a leader in the development of a number of conceptually-new trends in hydrogenerator design:
- a forced-air cooling system with transverse channels in rotor windings with an efficiency equal to that of a water-cooling system;
- a system that has a single layer in the slot parts and two layers in the end parts of the stator winding, for bulb type hydrogenerators with water cooling;
- direct water cooling of pole cores;
- stators with pre-tensioned cores, featuring high vibration resistance, stable dimensions and no residual deformations or pressing-out of core stacks;
- elastic seals of stator winding bars in slots, allowing for the prevention of slot discharges;
- a special design of stator and rotor end parts to avoid limitations during operation in under-excitation conditions.
All equipment undergoes necessary checks and testing at the factory before shipment. This makes it possible to optimize installation and commissioning timelines.
Power Machines’ hydrogenerators are equipped with the most reliable thrust bearings in the world. These thrust bearings are designed with a PTFE anti-friction layer using a metal-plated spring pad for bearing segment lining.
Advantages of Power Machines’ hydrogenerator thrust bearings:
- enhanced reliability and service life;
- do not require forced oil supply to the friction plane;
- no restrictions on operating conditions, including start-ups and shutdowns;
- allow for creeping speed and coast-down;
- allow for a specific pressure increase to 100 kg/cm2;
- allow for a reduction in friction losses and oil bath dimensions;
- do not require surface scraping during installation and operation.
- various types of hydraulic turbines;
- pre-turbine gate valves;
- the hydraulic part of governors and oil pressure units;
- automated control systems of hydraulic turbines;
- excitation systems and start-up frequency converters.
Power Machines offers the servicing, modernization and overhaul of HPP equipment, aimed at improved reliability, cost-effectiveness, control response and ease of operation.
By implementing power-plant overhaul and modernization projects, Power Machines meets strategic challenges ensuring return on customers’ investment by restoring the operating capacity of equipment and enhancing its technical and economic performance and reliability.
Equipment modernization and repair can be carried out at the manufacturer’s shop or power plant site.
Overhaul is planned and carried out in such a way as to minimize construction works and use existing embedded structures and foundations for modernized equipment installation as much as possible.
Catalogues
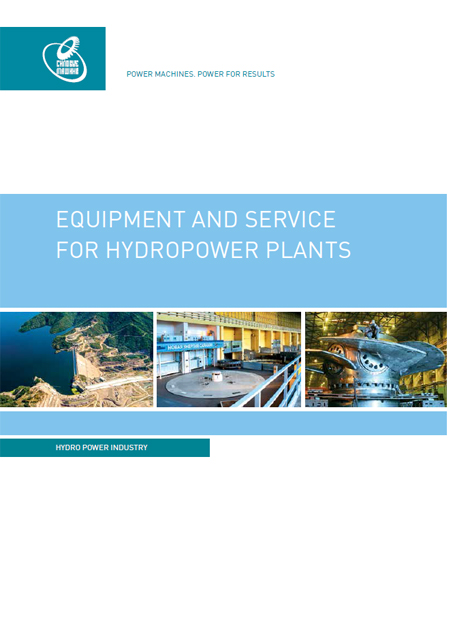
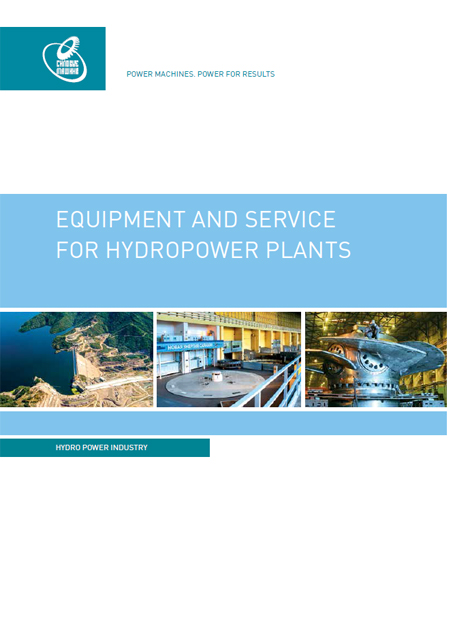
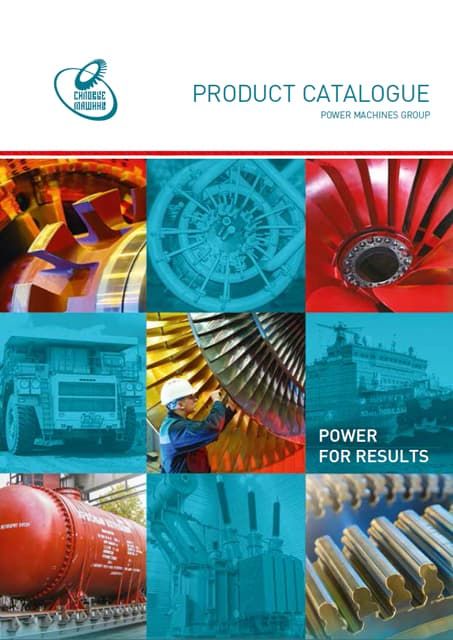
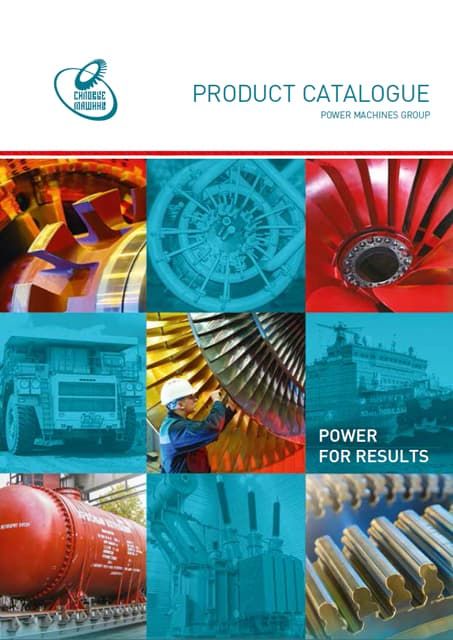
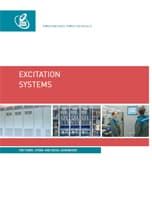
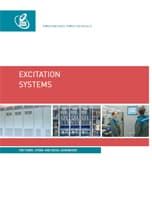
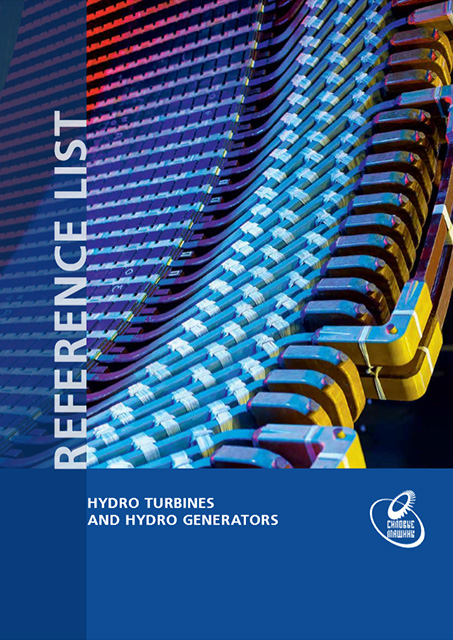
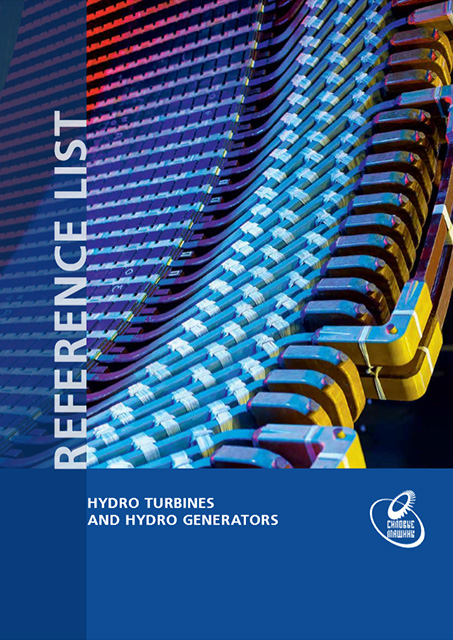