Transformers
- Series of two-winding transformers with split low-voltage windings (TRDN type in accordance with the technical requirements of GOST 12965).
- Series of two-winding transformers (TDN type in accordance with the technical requirements of GOST 12965).
- Series of three-winding transformers with split low-voltage windings (TDTN type in accordance with the technical requirements of GOST 12965)
- Two-winding main (generator) transformers.
- Series of two-winding transformers with split low-voltage windings (TRDN type in accordance with the technical requirements of GOST 17544).
- Series of two-winding transformers (TDN type in accordance with the technical requirements of GOST 17544).
- Two-winding main (generator) transformers.
- Three-phase autotransformers (ATDCTN type in accordance with the technical requirements of GOST 17544).
- Series of two-winding transformers (TDN type in accordance with the technical requirements of GOST 17544).
- Two-winding main (generator) transformers.
- Three-phase autotransformers (ATDCTN type in accordance with the technical requirements of GOST 17544).
- Three-phase autotransformers (ATDCTN type in accordance with the technical requirements of GOST 17544).
- Three-phase main (generator) transformers.
- Single-phase main (generator) transformers.
- Three-phase autotransformers (ATDCTN type in accordance with the technical requirements of GOST 17544) or as required.
- Single-phase autotransformers (AODCTN type in accordance with the technical requirements of GOST 17544) or as required.
- Three-phase main (generator) transformers.
- Single-phase main (generator) transformers.
- Three-phase autotransformers (ATDCTN type in accordance with the technical requirements of GOST 17544) or as required.
- Single-phase autotransformers (AODCTN type in accordance with the technical requirements of GOST 17544) or as required.
- High-voltage transformers plant has been created by two world’s leading power engineering companies – Power Machines OJSC and Toshiba Corporation, possessing a long track record of successful business practice, as well as production and developmental potential.
- The specialists of Toshiba Corporation carry out direct control in the sphere of product quality assurance, engineering and production technology compliance, and participate in resolving technical and production issues.
- The application of advanced design, engineering and production practices, implementation of a strict quality management system enable the joint venture to ensure manufacturing of reliable products with high operational characteristics.
Transformer magnetic cores are manufactured on the most advanced and fully automated cutting and stacking lines for electrical steel produced by a German company Maschinenfabrik Heinrich Georg, which also eliminate manual stacking and enable to make an efficient use of electrical steel.
Cut core is uniformly clamped by a binding clamp method, impregnated with insulating resin and subsequently heat treated. As a result there is an assembled magnetic system without stacking the upper yoke with previously assembled core legs, thus significantly reducing the level of mechanical stress on core plates.
Modern types of electrical steel are used for manufacturing magnetic cores. Prior to being used in production, electrical steel is tested in the plant laboratory for compliance with electrical behaviour and insulation characteristics stated by manufacturing plant.
The installed modern technological equipment, including a milling machining center and a throughfeed planer moulder produced by SCM Group s.p.a. (Italy), allow to produce a wide range of insulating parts with improved quality and accuracy characteristics.
The use of low-shrinkage thick cardboard sheets and wood laminates of the leading global manufacturers alongside with the high finish accuracy of automated processing centers enables to achieve high quality and assembling accuracy of complex insulating components during the manufacture of transformer windings and assembly of active parts, and also ensures increased electrodynamic resistance.
The use of modern vertical CNC winding machines as well as horizontal winding machines produced by an Italian company L.a.e. and fitted with accessories for decoiling, wire tensioning control, separate axial and radial pressing with preset force, ensures the production of windings of all types and designs with consistently high quality.
The windings are dried in vacuum drying cabinets produced by HEDRICH (Germany) using the technology of cyclic vacuuming at the stage of heating-up under a specific isostatic pressure.
The production of windings is carried out in production premises with controlled humidity and temperature where dust fall is constantly controlled.
Segmental assembly of windings as well the first and the second assembly of transformers of voltage class up to 750 kV is carried out in special “clean” rooms where dust fall is controlled.
All assembly works are performed with the use of lightweight, mechanical racks facilitating the mobility of production.
All transport movements are made by hover platforms.
Assembly of electrical scheme of transformer active parts is carried with the aid of a set of equipment used for preliminary forming and crimping of wires ensuring 100% control of all non-separable connections.
Drying of active parts of transformers is carried out in vacuum drying chambers produced by HEDRICH (Germany), applying the technology of vapour-phase drying with cyclic vacuum evaporation, under isostatic pressure on windings during drying.
Advanced equipment is used throughout the manufacturing of transformer tank metal structure:
- CNC plasma-arc burning centers;
- equipment for cutting bar sections;
- CNC machines for precise bending of sheet metal and tubes of circular cross-section;
- drilling-and-milling machines and lathes for mechanical processing of component parts.
In welding and assembly areas works are carried out with the use of :
- gas-shielded welding machines for welding with consumable and non-consumable electrode;
- mechanical units for welding of round and longitudinal seams.
Preparation and application of a coating on metal structures is performed in modern shot blasting chambers and painting-drying chambers.
Computer-aided measurement systems are applied at all stages of testing.
The test center is equipped with a powerful capacitor bank, high-voltage pulse generator and a powerful frequency converter with a frequency range of up to 50-200 Hz.
The installed systems enable to carry out high-voltage impulse testing, acceptance tests and temperature-rise tests.
The following components and materials are used:
- HV lead connections with RIP insulation;
- on-load tap changers with vacuum contacts;
- maintenance-free air dehumidifiers;
- quality fastening with hot dip galvanizing.
The service center of Power Machines Toshiba High-Voltage Transformers provides comprehensive services for the supplied equipment:
- technical supervision over works of assembly and installation, adjustment and putting into operation of power transformers within the warranty period;
- engineering supervision over the produced equipment during its whole service life;
- installation of transformers as part of contracts for the supply of equipment on a turnkey basis;
- technical supervision over repair works carried out on power transformers; supply of spare components;
- technical supervision over works on diagnostics of transformers;
- diagnostics of power transformers as part of turnkey contracts;
- gathering and analysis of information concerning the condition of power grid transformer fleet;
- participation in investigation of disturbances, failures and accidents of transformers;
- carrying out oil analyses in the plant laboratory in order to monitor the condition of power transformers during the whole period of operation;
- provision of training for customer personnel related to technical maintenance of power transformers during their operation.
Catalogues
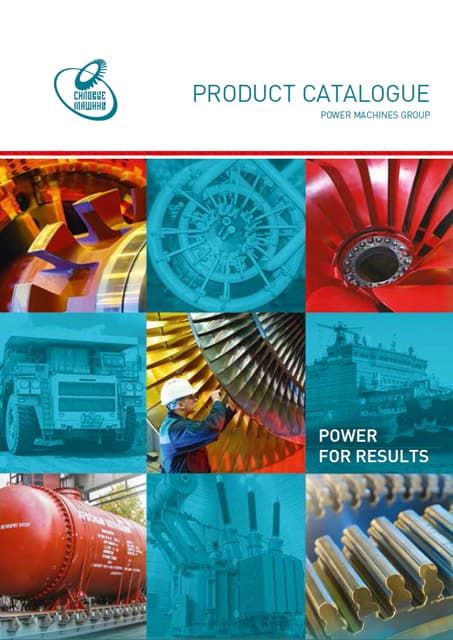
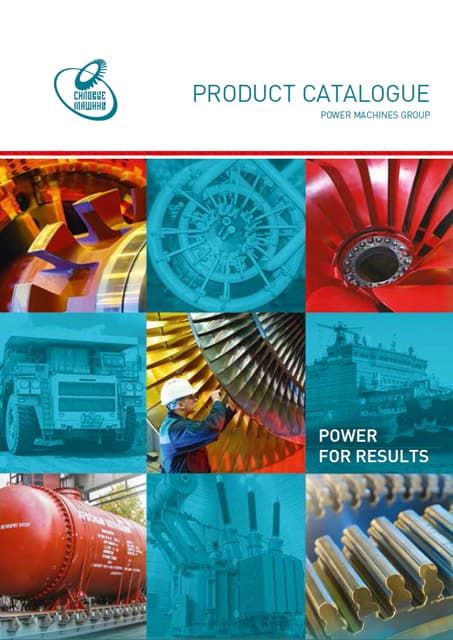